Motor Control Evaluation System Introduction Support Site
Sensorless vector control attracts attention by driving brushless DC (BLDC) motor (permanent magnet synchronous motor) at high efficiency and low cost.
This complicated control method is originally difficult to implement, yet with our easy-to-understand summarized procedure and tutorials, even beginners can start sensorless vector control within one day.
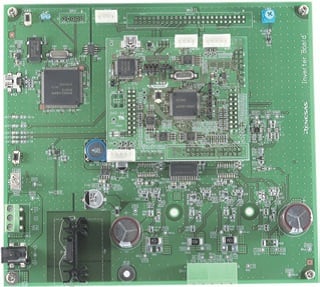
Evaluation Environment
Evaluation System for BLDC Motor
Evaluation Kit for Permanent Magnet Synchronous Motors (Brushless DC Motor)
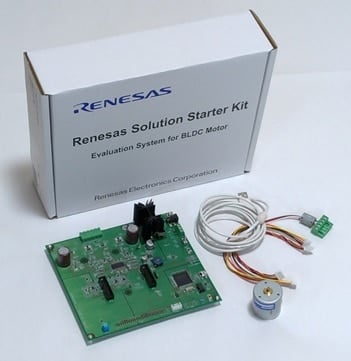
The Evaluation System for BLDC Motor is a solution kit for easily evaluating permanent magnet synchronous motors. When used in combination with a CPU card, various Renesas MCUs can control the motor. By using the Renesas Motor Workbench sample software and development support tool, evaluation and analysis can easily be performed, so you can start evaluation immediately after purchasing the kit.
Watch the introduction video and see what the kit can provide.
- Control rotation speed of BLDC motor simply by turning on power and volume resistor on the board. *1
- Various sample software released on our website can be used for program writing.
- By connecting PC and board with USB, motor control parameter can be displayed real time on PC in an oscilloscope-like graphic form (increase debugging efficiency, shorten development period).
- Since it is possible to check operation while changing parameters, it is easy to evaluate and optimize the control algorithm using RSSK platform.
- Auto-tuning (both motor characterization and control parameters estimate) are achieved with simple steps.
*1 There are two ways to rotate the motor with this kit- board switch and volume resistor operation & Renesas Motor Workbench. In the initial status when the kit was purchased, operation from the board is set as default program, and operation from Renesas Motor Workbench is the default of the sample programs published on our website. These operation methods can be switched. For more details, please refer to the sample program application notes.
Development Support Tool
Renesas Motor Workbench
Motor Control Development Support Tool
Motor control contains various know-how and adjusting, debugging often requires a large number of man-hours and expenses. By using Renesas development support tool - Renesas Motor Workbench, these problems can be solved and excellent cost-to-performance ratio can be highly expected.
Renesas Motor Workbench 3.0 was released in December 2021. We have added an Easy GUI for easier operation and updated the existing User buttons and Commander functions. Please also refer to the following video regarding the new features.
Analyzer
Visualization increased debugging and evaluation efficiency!
- Writable variables & real time waveform display
- Display, trigger setting control parameters in an oscilloscope-like graphic form
- Action profile creation, analysis and manipulation are possible
Tuner
Auto-adjust parameters for vector control with no specialized knowledge needed!
- Auto-extract motor parameters such as resistance and inductance, and control parameters such as PI gain by entering rated current and number of pole pairs of the motor and pressing Start button
- Immediate usage of output parameters for motor rotation and fine adjustment is possible. Final result can be output to header file
* Tuner feature is not applicable to RL78 family.
* Motor control development support tool is not applicable to RL78/G1G.
Easy GUI
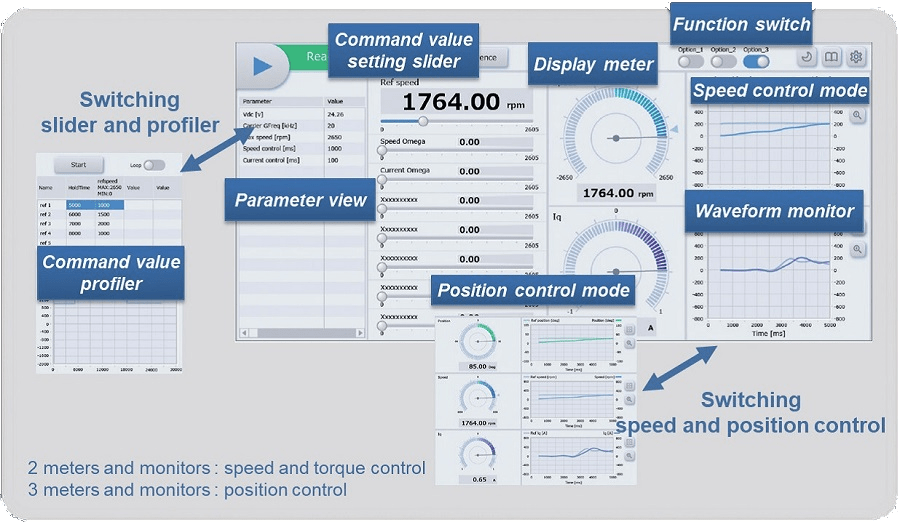
Implemented a GUI for more intuitive motor operation
- The command values can be set using a slider
- The command value profiles can be set
- Display of rotation speed, current value, etc. on the meter
- Switch for switching functions
- Waveform display of variable changes
- Display of various parameters
Evaluation Kit / Tool Demonstration
1. Renesas Motor Workbench [Set-up]
- PC software installation
- PC to board connection
2. Evaluation System for BLDC Motor [Set-up]
- Introduction of what's included
- Board connection
3. Motor Control Software [Download]
- Connection of CPU card and E2 Emulator Lite
- Obtain sample software
- Build sample software in CS+
- Write the microcontroller program
* E2 Emulator or E2 Emulator Lite is required to write programs
4. Renesas Motor Workbench Analyzer [Basic]
Display motor control internal variables in an oscilloscope-like graphic form!
- Display and rewrite microcontroller internal variables
- Real-time waveform display of microcontroller internal variables
5. Renesas Motor Workbench Tuner [Basic]
Sensorless vector control is immediately possible with no know-how required!
- Auto-adjust parameters for sensorless vector control
- Motor control using extracted parameters
6. Renesas Motor Workbench Analyzer + Tuner [Application]
Adjust motor control parameters by monitoring the motor’s behavior and internal variable waveform at the same time
- Display waveforms of trigger set internal variables during motor start up
- Confirm reference speed value and motor rotation speed
- Change control parameters and control traceability and stability
7. Renesas Motor Workbench Analyzer Math function
Additional display of user-defined operation waveforms in the waveform-displayed variables!
- Displays waveforms with various operations on channel values
- Between channel operations and display of operation values only are also possible.
Supported operations: Delay, sine, cosine, tangent, inverse tangent, square root, power, multiplication, division, addition, subtraction
8. Renesas Motor Workbench Analyzer Status Indicator
The system notifies you with a change in the rotating light color when a variable matches a user-defined condition (variable + threshold condition)!
- Multiple variables can be monitored.
- Multiple conditions can be set for one variable.
- Information that matches the conditions is displayed as a log on the list screen.
9. Renesas Motor Workbench Analyzer Increase the number of waveform display candidate channels
Easy switching of variables to display waveforms!
- Maintains a large amount of user-configured channel information
- Waveform display is switched ON/OFF in Check Box [Use].
10. Renesas Motor Workbench Analyzer Alias Name
User-defined aliases for variable names whose meaning is confusing!
- Change display of long or confusing variable names to aliases
- Switching can be set for each variable
- Japanese display also works
11. Renesas Motor Workbench Analyzer USER BUTTON
Multiple operations are just one click away!
- Finely detailed sequences can be created, such as simultaneous execution
- Internal variables can be used to write values as they are read
12. Renesas Motor Workbench Analyzer COMMANDER
Register variable Write and interval for sequential operation!
- Perform sequential writes
- Interval spacing can be set
- Repeated (loop) processing is possible
13. Renesas Motor Workbench Analyzer ONE SHOT
Programmatically buffered data on waveform display!
- Buffered data can be displayed as a waveform
Scale and offset settings are available
14. Renesas Motor Workbench Analyzer Navigation
New function in RMW3.1
Spend less time reading manuals! Check the procedure for RMW function while using
- Display instructions for RMW functions such as User Button, Commander, Status Indicator and Tuner within RMW
15. Renesas Motor Workbench Analyzer Parameter Output
New function in RMW3.1
Output the adjusted control parameters as a header file and easily reflect them in the program
- Output adjusted variables to header file as macro definitions
- Select a variable to be linked to a macro definition
- A new macro name can be added to the end of the file for output
16. Renesas Motor Workbench Analyzer Variable Meaning
New function in RMW3.1
Variable usage information can now be displayed on Control Windows
- Display usage information of variables by reading CSV files
- Usage information can be used when searching for variables
17. Renesas Motor Workbench Servo Function
New function in RMW3.1
Simple servo control operation on GUI
- Inertia Estimation: Estimate the rotor + load inertia connected to the motor shaft
- Servo Turning: Parameter adjustment for position control and control frequency
- Return to Origin: Set the return to origin method and return speed
- Point to Point: Set the PTP (Point to Point) and operation checking
18. Renesas Motor Workbench Easy GUI
Makes it easy for anyone to drive and debug motors
- The intuitive operation allows anyone to easily control the motor speed and position
- Motor operation status is displayed by meter and waveform
Software / Application Notes
Integrated Development Environment (CS+, e2 studio)
*Includes free evaluation version for linkable object size under 128KB.
Motor Control Development Support Tool "Renesas Motor Workbench"
[document:1023176]
Application Notes
Sample code and application notes for each type of motor control. My Renesas ID is required.
24V Motor Control Evaluation System for RX23T
Permanent magnet synchronous motor (brushless DC motor)
RL78/G1F Sensorless BLDC motor initial rotor position detection Software & Application notes: Sensorless detection of initial position of the rotor Rev.1.10 (PDF | English, 日本語)*3
*1: Uses partner board.
*2: For obtaining information, please contact sales / distributor.
*3: To operate the program targeted by this application note, it is necessary to modify the circuit of Renesas Solution Starter Kit 24V Motor Control Evaluation System for RX23T. If you modify the circuit, other programs for Renesas Solution Starter Kit 24V Motor Control Evaluation System for RX23T will not be able to operate Regarding circuitmodification, we do not guarantee the operation of this program after amendment.
*4: Two types of timer (MTU / GPT) setting are implemented as PWM output timer, and it can be selected at compile time.