Motor control is used in a wide variety of household appliances and industrial equipment, and its usage continues to increase yearly. To maximize the performance of motor control, it is essential to have accurate position information. Although sensors are used to detect position, sensorless control methods (also known as position sensorless or sensorless) have become mainstream due to concerns about sensor maintenance, cost, reliability, and environmental resistance.
However, conventional sensorless methods rely on algorithms that estimate position information from the induced voltage generated by the motor's rotation. When the motor's speed is low, the induced voltage is also low due to the motor's physical characteristics, making it difficult to accurately obtain position information and apply sensorless vector control (Field Oriented Control: FOC) at low speeds. This time, we introduce the "whole speed range position sensorless FOC" solution that enables the application of sensorless FOC at all speeds. The solution allows efficient control at all speeds, contributing to lower power consumption and improved product performance. In this solution, we use the RX66T, an RX product designed for motor control applications.
Motor for Whole Speed Range Position Sensorless FOC
To take advantage of this solution, it is important to understand the types and features of the motors. There are two main types of permanent magnet synchronous motors (brushless DC motors): interior permanent magnet synchronous motors (IPMSMs) and surface permanent magnet synchronous motors (SPMSMs). These motors have different characteristics due to their different magnet configurations. In particular, IPMSMs have a unique feature in which their magnetic resistance varies depending on their rotational position (saliency). This saliency allows for highly accurate position information acquisition even at low speeds, which is the key to enabling sensorless FOC across the full speed range.
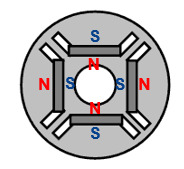
IPMSM
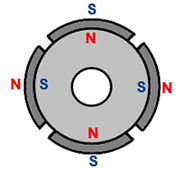
SPMSM
Advantages and Disadvantages
The whole speed range position sensorless control solution has both advantages and disadvantages, and it may not be suitable for all applications. Here, we introduce the advantages and disadvantages of the solution and compare it to conventional sensorless FOC, which typically uses open-loop control without feedback at low speeds.
Category | Conventional Sensorless FOC | Whole Speed Range Position Sensorless FOC |
---|---|---|
CPU Load, Memory Size | Better | Worse (slightly higher than conventional sensorless) |
Power Consumption | Higher | Lower |
Startup Time | Slower | Faster |
Low-speed Load Operation | Impossible | Possible |
High-speed Load Operation | Equally | Equally |
Noise | Better | Worse (Harmonic noise at low speeds) |
Applicable Motor | Wider (General PM motor) | Narrower (IPMSM only) |
The benefits of whole-speed range position sensorless control include lower power consumption, stable torque output at low speeds, and faster startup. Conventional sensorless control typically requires a forced excitation process for magnet attraction and position fixing, resulting in slower startup and difficulty handling loads above a certain level. However, using IPMSMs with whole speed range sensorless FOC allows for accurate initial position estimation, enabling faster and more stable startup than conventional sensorless control.
On the other hand, the increasing CPU computational processing and the presence of harmonic noise during motor operation are among the disadvantages. The harmonic noise may be audible to users and may not be suitable for applications in quiet environments. Additionally, not all PM motors are applicable, as only IPM motors with saliency can be used. This solution requires a minimum of 20% difference in the d-axis and q-axis inductance.
To summarize, the whole-speed range sensorless motor solution may not be as effective for applications where high-speed rotation is the primary focus, and noise-sensitive applications may require additional considerations or measures. However, it is highly suitable for applications operating at low speeds, battery-powered applications where power consumption is a concern, and outdoor or factory environments where noise impact could be minor. In such a case, this solution enables sensorless FOC to be applied in speed ranges that were previously unattainable.
Target Applications:
- Pump
- Conveying System
- Compressor
- Home Appliances
Whole Speed Range Position Sensorless Motor Solution
The whole speed range position sensorless motor solution offered by Renesas includes an application note and sample software for the RX66T CPU card. It is implemented using our partner's inverter board and commercial IPM motors, allowing you to quickly set up an evaluation environment. We hope that by taking advantage of this solution, you can gain a hands-on understanding of the motor's characteristics, fine-tune parameters, and implement it in real-world applications, thereby facilitating the development process.
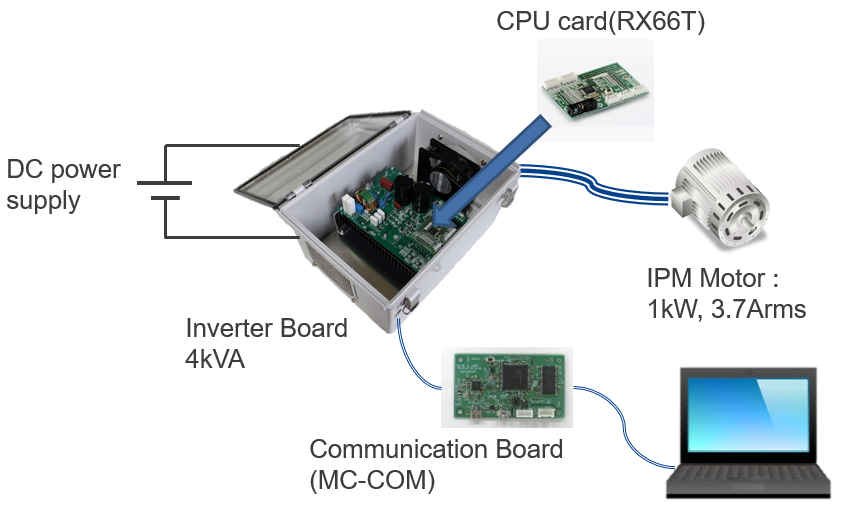
System Configuration
For more details on the whole speed range position sensorless solution, please refer to the following:
- Whole Speed Range Sensorless Motor Solution
- RX Family Sensorless Vector Control for IPMSM over the Whole Speed Range Rev.1.00 (PDF | English, 日本語)
- RX Family Sensorless Vector Control for IPMSM over the Whole Speed Range Rev.1.00 (ZIP | English, 日本語)
In Conclusion
The solution presented here employs the RX66T for position sensorless FOC across the entire speed range. If you're considering FOC for all speed ranges, as well as improvements in power consumption and efficiency, we encourage you to leverage our solution. Alongside the featured solution, the RX-T series, including the RX66T, offers sample code and application notes for sensorless FOC with SPMSMs and encoder-based FOC. Please refer to the "Documentation" table below and consider exploring these solutions as well as experiencing motor control using RX products.
Documentation
|
|
|
---|---|---|
Type | Title | Date |
Application Note | PDF 3.17 MB 日本語 | |
Application Note | PDF 2.73 MB 日本語 | |
Application Note | PDF 2.16 MB 日本語 | |
3 items
|
Downloads
|
|
|
---|---|---|
Type | Title | Date |
Sample Code |
[Toolchains=CC-RX|V3.06]
ZIP
150.22 MB
日本語
Application:
Industrial
Compiler:
CC-RX
Function:
Application Example
IDE:
CS+ for CC, e2 studio
|
|
Sample Code |
[Software=RX Smart Configurator|v2.15.0],[Toolchains=CC-RX|v3.04.00]
ZIP
15.65 MB
日本語
Application:
Industrial, Renewable Energy & Grid
Compiler:
CC-RX
Function:
Application Example
IDE:
CS+ for CC, e2 studio
|
|
Sample Code | ZIP 80.40 MB | |
3 items
|