Electric motors are found in various industrial environments. Industrial automation systems have developed over the years and production lines have relieved humans from the hardest and most dangerous tasks. These systems largely rely on motors to accomplish different functions, from moving parts to fine assembly. Warehouses are also using robots as well as collaborative robots (CoBots) to stock or ship goods.
Besides these industrial environments, the presence of electrical motors surrounds everyone’s daily lives. Just think about all the home appliances – like refrigerators, vacuum cleaners, air conditioners, toys, small electrical vehicles (like E-scooters), and other appliances and devices that all use electric motors to convert electrical energy into useful mechanical energy.
Choosing the Right Motor
Nowadays, there are a large variety of electrical motors. DC motors are among the most popular and well-known, as they represent one of the most cost-effective options available. However, these types of motors have a few drawbacks, which don’t make them ideal for several applications. One drawback is that DC motors use carbon brushes to connect the motor coils and generate the rotating magnetic field. Over time, motor brushes wear out, compromising the function of the motor.
Brushless DC motors (BLDC) solve this problem by removing the brushes, but it still needs additional components to properly perform motor commutation functions. Sensorless technology uses highly sophisticated techniques to perform BLDC motor commutation without requiring sensors to determine the position of the rotor. These techniques do a great job and do not add extra costs, weight and assembly burden for sensors, and do not require additional space in the motor. However, in certain applications, sensorless technologies cannot satisfy requirements if very high torque at start up is required. In addition, if very precise positioning of the rotor is needed (e.g. robots), sensorless technology cannot achieve high resolution and accuracy. In general, sensor-equipped technologies used in motor commutation applications can overcome these issues and improve performance in terms of efficiency, less vibration, less acoustic noise, and smoother torque control.
Another very popular choice of motor is a stepper. This kind of motor offers high torque at low speeds. Because of their rugged construction, they can operate in almost every environment without durability issues, as steppers do not have brushes. By using cost-effective off-the-shelf standard inexpensive electronics, steppers are very useful for high-precision positioning without needing any external sensors. Compared to BLDC motors, sensorless motor commutation for stepper motors reaches its limits if high efficiency and/or high torque are required.
Choosing the Right Sensing Technology
If motors must be equipped with sensors for positioning or motor commutation, there are basically four main options: discrete Hall switches, integrated magnetic encoders, optical encoders, and resolvers. Each of them offers a list of pros and cons. The simplest technology is represented by discrete Hall switches, which only offer a basic kind of motor commutation: the block commutation. This solution can only be used in simple applications that do not require any precise positioning of the rotor. In contrast, in several ambits, integrated magnetic technology is still a very popular choice. Even though these sensors are very robust, can work in harsh environments and offer both absolute and incremental analog or digital interfaces, they cannot be used as off-axis sensors (e.g., through-shaft or side-shaft), meaning that one side of the shaft must be reserved for the sensor and the magnet. This is a big limitation for this technology. Applications that demand off-axis sensors can use either optical sensors or resolvers. The former can achieve very high resolution and accuracy, but unless they are encapsulated, which makes it very expensive, they are very sensitive to harsh environments when it comes down to high temperature, humidity, vibration, and dust. The latter is very robust, but besides being very bulky and heavy, does not represent a cost-effective solution.
The Most Efficient Solution for Motor Commutation Applications
To address this big challenge in motor commutation, Renesas has developed a new technology based on inductive position sensing that can overcome the common trade-offs of the standard technology and combines the off-axis capability with very affordable costs.
In Renesas’ inductive technology, the sensing element is represented by a set of coils designed on the PCB. One major strength is the possibility to design the sensing element around the customer application. By matching the number of sectors of the sensor to the number of pole pairs of a BLDC, it is possible to boost the sensor accuracy at the maximum. With a sine/cosine output interface, this solution can achieve superior accuracy than other well-established sensing technologies (such as magnetic encoders), as well as reduce the size and weight of the device at a much lower cost if compared to resolvers.
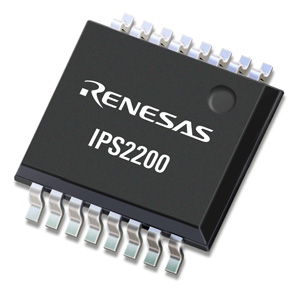
The IPS2200 product is a position sensor based on Eddy currents and can deliver the absolute position as demodulated sine/cosine within one electrical rotation. The IPS2200 represents a new era in motor commutation and will define the next benchmark in the industry.
Visit the position sensor page to learn more about how Renesas’ inductive technology can help with your design.